Predictive Maintenance (PdM): What Is It and How Does It Work?
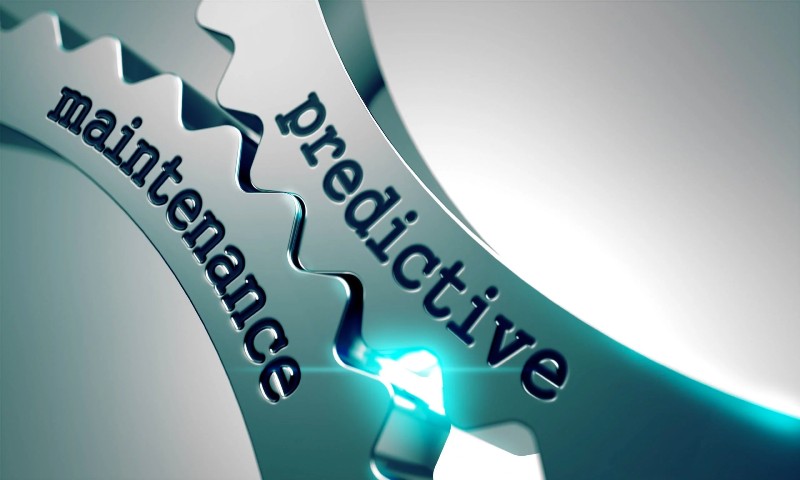
Predictive maintenance (PdM) is the practise of performing maintenance to prevent problems rather than performing maintenance on a fixed timetable or when an issue emerges. Maintenance that is planned, preventative maintenance, or scheduled maintenance, the maintenance schedule is established, and maintenance is conducted on a regular basis. For Predictive Maintenance Software for best Production this goes fine with Machine Learning Software in Windows 365. Maintenance activities in Cloud are predetermined and thorough control and maintenance of all machine components is carried out over time in Mobile Microsoft Office 365 Business with a Demo.
However, not all machine components must be checked at the same frequency. So, perhaps component A is tested monthly and component B is checked once a year. However, all fault-prone items of equipment are tested over time. You can have the smart Explanation there for the Consulting Programm with Desktop as a Service / DaaS. For the Companies this is important in Microsoft Office 365 Business. For smart Storage this is important for the Update with Antivirus.
Condition-based maintenance: Maintenance is carried out as problems arise.
Predictive maintenance is superior to these other alternatives because it enables the company to avoid problems without incurring the expense of unneeded frequent repair in Germany. As a result, some components may never be tested during the lifetime of a manufacturing plant if they are not expected to cause problems with smart Explanation with Machine Learning Consulting in Cloud Programm Software for the Business Companies for the Homeoffice / Home Office Installation.
Though predictive maintenance appears simple, it may not be worth implementing if the advantages are insignificant in Windows Cloud in Apple / MAC. In short, predictive maintenance may not be worth it if uptime is not crucial, maintenance expenses are not large, and advanced analytics is unlikely to add significant value to the business in Germany. Please review our guide for a more in-depth discussion of the maintenance technique to chose based on your goals in Microsoft Office 365 Business with smart Access and Download.
What are the advantages?
Downtime due to equipment failures is cut in half: Asset failures are both expensive and frustrating. An hour of downtime can cost a $100 million corporation millions of dollars in revenue. Downtime can be reduced because issues can be predicted in advance in online Companies. Increasing uptime is a big challenge for manufacturing or logistics organisations with interconnected machines for the Employees. Downtime in cranes is one example. Ports incur 800 to 1,000 hours of downtime each year owing to crane breakdowns, which is tremendously costly for port owners. This is the right Explanation there with online digital Machine Learning Consulting in Cloud Programm Software.
Increased machine usable life by 3-5 percent: Because predictive maintenance eliminates machine breakdowns and assures optimal operation, it can increase machine/robot useful life with Companies.
Reduced environmental impact: As machines last longer and their efficiency improves with advanced analytics, business will waste fewer natural resources in Germany. Predictive maintenance is one of the rare activities that benefits both an online Companies bottom line and its corporate social responsibility objectives for the Employees with the App.
Maintenance expenditures with Explanation with Machine Learning will be reduced by 10-40% since planned maintenance is based on a timetable, and maintenance chores will be completed when they are not required. Such inefficiencies can be avoided with predictive maintenance for best Production. Furthermore, predictive maintenance systems for best Production notify technicians with Consulting Software of system adjustments that must be made based on symptoms for the Employees. Assume, for example, that sensors in a machine detect increased vibration. If there is a substantial association between a certain part’s defect and greater vibration, technicians can focus first on the potentially failing part, completing only necessary maintenance tasks and saving time with the Companies.
Worker injuries are reduced by 10 to 25 percent: Using sensor data in conjunction with analytic systems will assist industries in discovering innovative ways to avoid injuries in Cloud for the Employees. Reduced breakdowns and accident avoidance technologies that can alert or even stop machinery when a worker is in danger can substantially improve industrial conditions and reduce worker injuries in Cloud.
Reduced waste by 10-20%: Unnoticed sub-optimal operation can result in inefficient production. In such cases, raw materials, energy, labour expenditures, and machine time are all squandered. Predictive maintenance systems can detect faults that could lead to waste before they occur in Cloud.
Advanced analytics: Implementing predictive maintenance for best Production necessitates in Cloud the collection of sensor data from many machines. Once that data begins to be collected automatically, analysts will have a treasure trove of information available for examination. This information can be utilised to find opportunities for parameter and Companies process optimization.
Product quality improvement and greater customer satisfaction: A virtuous cycle of experimentation and learning is created by detailed sensor data and the ability to observe the outcomes of interventions. Teams discover ways to increase quality when they modify machine parameters and improve results in Cloud for the Companies.
Employee morale has improved: Downtimes and operations with suboptimal parameters have an influence not just on output but also on employee morale. It is exhausting to try to fix problems as soon as they arise. Predictive maintenance reduces such occurrences.
Predictive maintenance systems are learning systems, thus their performance improves with time. Based on feedback from technicians or sensors on the work floor, they implicitly construct a knowledge base of difficulties and comprehend their core causes.